机床被称为“工业母机”,是装备制造的重要基础,没有机床的智能化,就无法实现装备制造业的智能制造。刀具作为机床的“牙齿”,其性能和质量直接影响机床生产效率的高低和加工质量的好坏。近年来,随着产业结构升级以及高端制造等国家战略的推进,各项国家鼓励政策的推出为我国刀具行业健康、稳定的发展奠定了政策基础。
国家统计局发布的《战略性新兴产业分类(2018)》将切削刀片深度加工和数控刀片列为重点产品和服务。此外,2019年10月,国家发改委发布的《产业结构调整指导目录(2019年本)》明确将“高档数控机床及配套数控系统:五轴及以上联动数控机床,数控系统,高精密、高性能的切削刀具、量具量仪和磨料磨具”列为鼓励类产业。受益于国家政策的鼓励和扶持,数控刀具行业迎来了新一轮快速增长周期。
自2016年以来,全国刀具消费总额呈现快速增长态势,由2016年的321.5亿元增至2018年的421亿元,年平均复合增长率达14.43%。但由于缺乏信息管理等原因,刀具往往存在使用混乱,资源浪费的现象,同时由刀具磨损带来的加工精度降低,表面粗糙度和表面层质量等指标下滑,直接影响加工的效率、质量和成本。
研究表明,由于刀具磨损和破损而造成的机床停机时间占全部停机时间的20%。而有效的刀具监测系统能提高加工效率10%~50%,降低生产成本10%~40%。因此,实现刀具的在线监测,建立完整的刀具数据库管理系统,具有重要的意义。
目前,刀具磨损监测大致可分为直接监测和间接监测两种方式,直接监测主要通过光学图像法、接触式电阻测量法和放射性元素法等手段实现监测。直接监测法虽然监测精度高,但大部分情况需在切削过程的间隔进行离线监测,造成切削过程的不连续性,不利于在实际中应用。
间接监测则是通过分析噪声、削力、振动、声发射、电机电流与功率等,间接获得刀具的磨损情况。相较于直接监测手段,间接监测手段无需在设备停机或者切削过程间隔中监测,实际应用机会多。
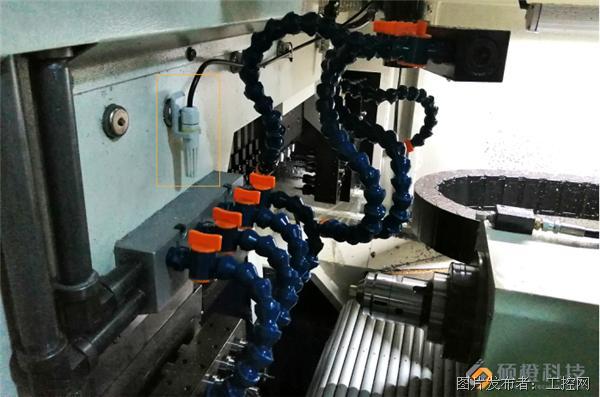
CNC数控机床刀具现场安装图
//产品介绍
硕橙科技“机器听诊大师”通过非接触式的方式,采用独创的噪声特征集系统,实时收集、分析加工过程中刀具与工件接触产生的噪声,解决传感器安装限制。
通过加工模板库的建立,实时量化评估刀具磨损度、加工完成度,并在发生断刀、崩刀等异常情况时及时报警。此外,系统也可应用于刀具研发领域,辅助刀具材料、参数调优等试验。
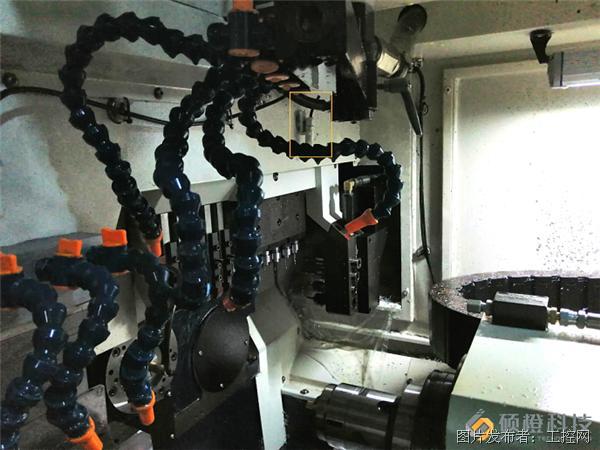
CNC数控机床刀具现场安装图
//产品优势
1.非侵入式安装,无需介入设备;
2.集成机器学习与AI算法;
3.边缘计算,低数据量,高实时性;
4.可复用的故障模型库,实时评估设备运行情况。
//产品功能
1.按时间自动统计机床设备运行状态;
刀具监测终端可追溯刀具的使用记录,对刀具运行状态进行统计,有效分析刀具使用情况。
2.实时监测机床整机、辅机等运行状况;
3.自动识别标记加工零配件、刀具型号;
系统自动识别不同的加工零配件以及刀具,根据每个工件及刀具的独特噪声特征值,对刀具的加工过程进行监测。
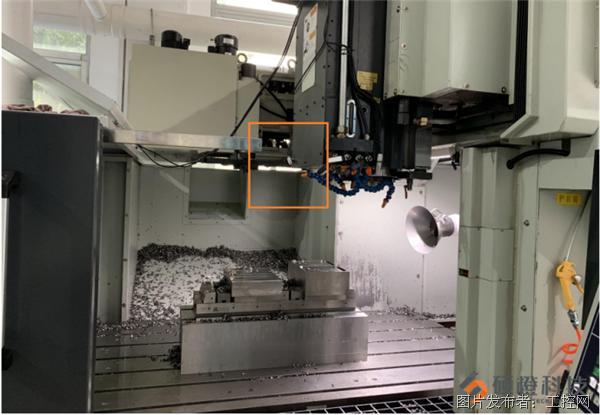
刀具加工区域现场安装图
4.发生断刀、崩刀等异常事件及时报警提示;
当异常事件发生时,系统自动推送异常报警及包含故障信息的短信,提醒工作人员及时维修,有效避免故障恶化。
5.刀具研发试验针对加工参数、材料质量进行测评;
对刀具的加工使用参数进行评分测试,对刀具材料进行测试并进行刀具材料状况评估。
6.在线刀具生命周期管理,实时反馈加工刀具磨损情况,提高刀具利用率,降低备件成本。
//实际案例:某大型制造企业数控机床
该台机床加工零部件种类较多,有四十多种,由于国外厂商未开放数据接口,企业对机床的实际加工情况无法掌握,只知道整条产线的加工总量。
硕橙科技通过对不同零部件整个加工过程中噪声行为的建模和适配,帮助企业实现了对加工零件类别的实时判别,并对每次加工进行打分,同时加工刀具出现异常时的实时报警也使得企业能够做到预测性维护,最大程度提高生产效率,降低成本。
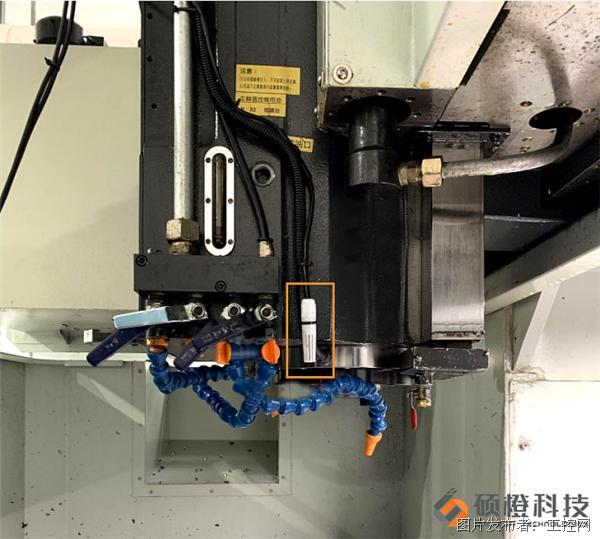
拾音探头现场安装图