在现代化的汽车生产车间里,数字化和智能化技术为突破传统制造工艺中的难点打开了全新思路。
以冲压工艺为例,振动直接反映着加工过程中的设备健康状况,是设备安全评估的一项核心指标。然而,振动分析极为复杂,产线上多种设备和众多组件之间的振动相互影响、叠加,形成一场大型“复合”振动,只有经验丰富的领域专家才能“读懂”这些动态交错的信号。但专家无法全天候实时监测,尤其在伺服压机应用场景中,速度、位移、压力等都在不断变化,单凭人力更难以捕捉复杂的加工过程。当人力不可为,人工智能介入是必然选择。
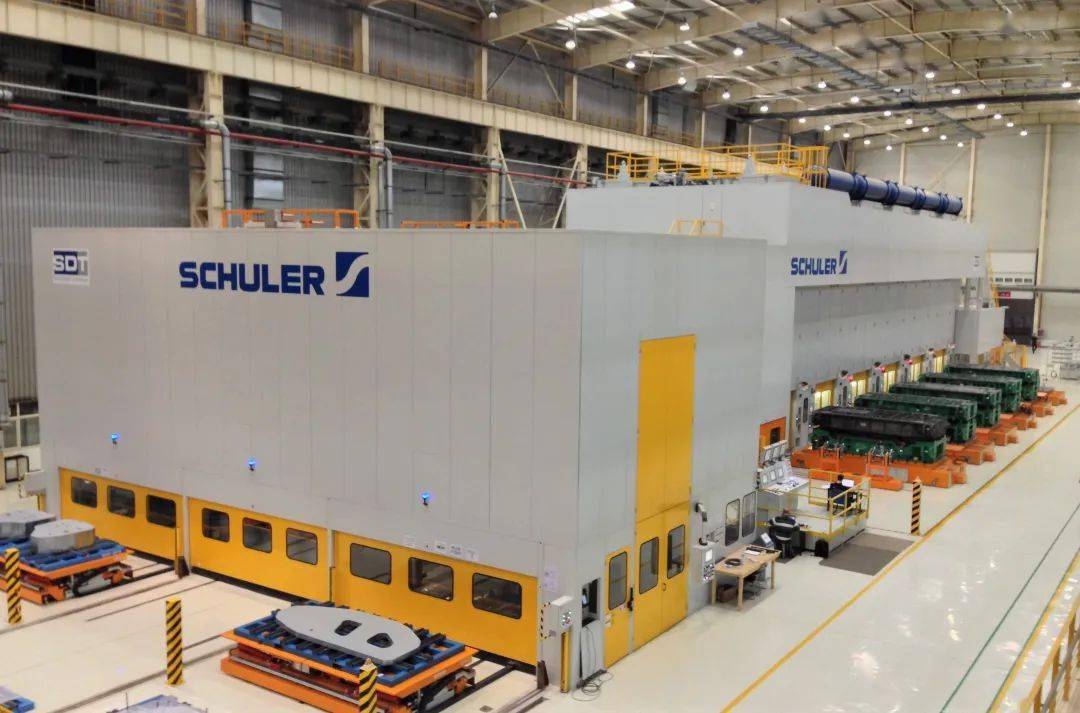
北京奔驰与西门子合作,以人工智能、云计算等数字化技术打造智能制造车间。
来自西门子数字化工业集团客户服务部门和西门子中国研究院的专家团队,将专家经验与人工智能相结合,实现了基于振动分析的预测性维护。北京奔驰汽车有限公司(北京奔驰)与西门子合作,为其冲压车间(一期)生产线上的关键设备加装了70多个传感器,每个传感器每秒可采集20000多个数据点。如此庞大的数据量上传至云端,进行基于机器学习技术的云端大数据分析。“聪明”的人工智能系统因此成为了专家智慧的延伸,能够实时掌握设备状态,并预测未来一段时间内出现故障的可能性。
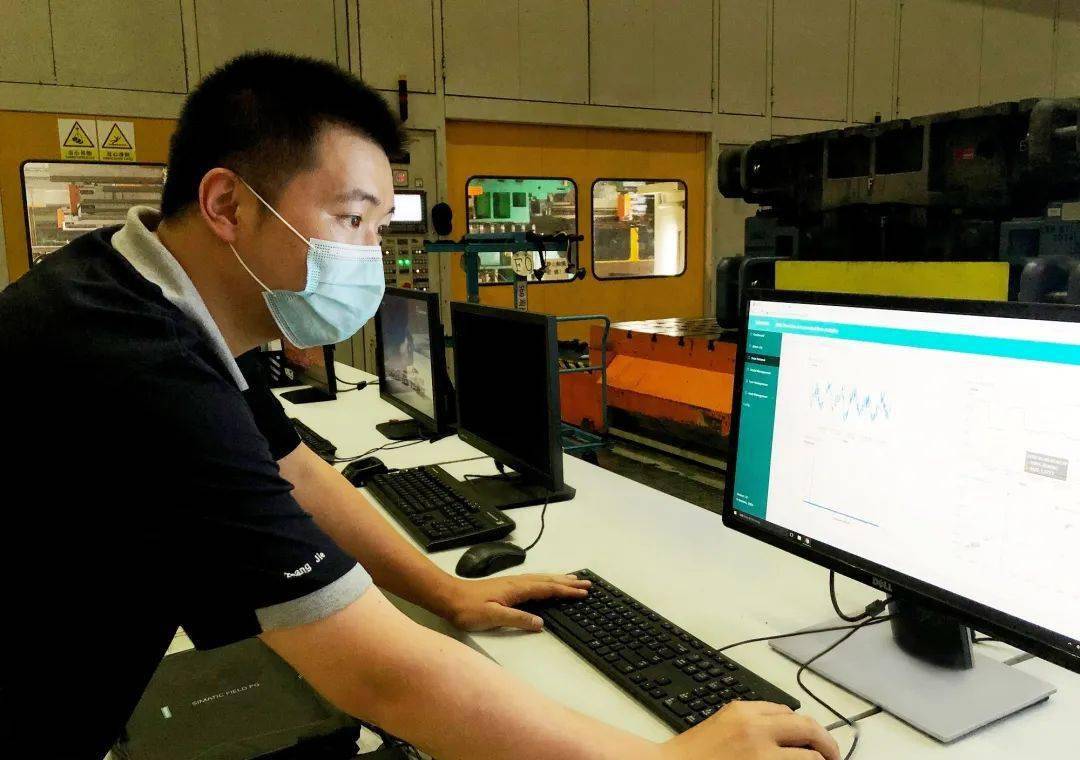
有了人工智能的加持,针对加工过程中的振动分析会更加精准且全面,帮助工作人员高效安排运维工作。
“成功部署后,系统在一天深夜捕捉到车间某处电机异常振动,即时通知客户,避免了非计划性停机,保证了产线的正常运行。”西门子中国研究院高级研究员周林飞说,“未雨绸缪,这让大家切实感受到了工业人工智能的价值所在。”